Healthcare construction projects—particularly renovations—call for careful consideration of many critical factors, from infection control and life safety to the experiences of the patient, family and caregivers. Jay Bangert, CHC, LEED AP BD+C, project executive, and project managers Ben Stuby and Tyler Musgrave, CHC, have all worked extensively in operational hospital environments. They offer the following guidance for healthcare owners preparing to embark on facility improvements.
What considerations should owners and operators of healthcare facilities keep in mind as it relates to safety, infection control, and a smooth process during their construction expansions and renovations?
Tyler: When planning for work in an active hospital, patient safety needs to be the number one priority. Safety and infection control go hand-in-hand. It’s important to view challenges from a high, comprehensive level, to have a master plan, and maintain flexibility. The most successful planning occurs when all parties understand the goals and are clear on the work to be completed.
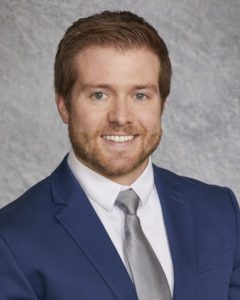
When doing any top-to-bottom renovation where functions and patient care areas will be relocated, it’s also important to make sure the scenarios are well thought out. Work should be clearly conveyed on the Infection Control Risk Assessment (ICRA) and Interim Life Safety Measures (ILSM). These documents should specify who will be affected and who to notify.
Document management should be consistent, and both construction team members and facilities personnel need to understand how utilities are fed to maintain operations outside of the project area.
Ben: Successful renovations start with a detailed and accurate phasing plan. Before any temporary infection control barriers are constructed, it’s critical to understand how the staff is currently accessing areas of the hospital. While the design team may have concepts for phasing, the actual conditions for constructability need to be reviewed.
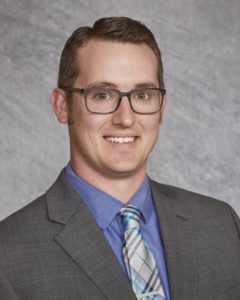
In addition, the project team should take a detailed look at where corridors connect and how egress (exit points) can be maintained. In public areas like hospital lobbies, multiple corridors often intersect at a single point, so work on the finishes in that area may have to wait until other routes can be established or, if applicable, completed during off-hours.
You have to weigh the cost impact of an area being down temporarily versus how quickly it’ll re-open as a result. We can provide options that help healthcare organizations run the numbers and determine what is going to be most effective for their goals.
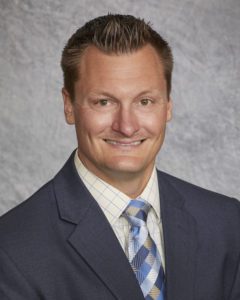
Jay: During the pre-construction phase of a renovation-in-place, usually my first question to the user groups is, “What is the smallest amount of space you can live in while the renovation surrounding you takes place?” The more room the contractors can have, the less incremental and more efficient we can be with phasing.
After we understand what the users need and what support space they require, we review how existing utilities are fed and what new systems are going into place. The systems piece can be the most complicated part of the renovation, from relocating electrical and data rooms to replacing air handling units.
How does Hagerman get involved in helping clients with their Interim Life Safety Management Plans? What is required of hospitals when putting one together and training people on it?
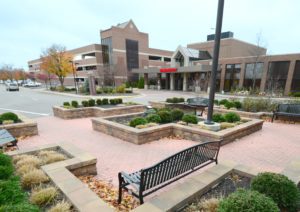
Jay: It’s always best for us to get involved early so we can better understand which will work better—a built-in-place infection control wall or a modular wall system. In addition, as we walk through the main mechanical, electrical and plumbing (MEP) infrastructure within the project, we can plan how we’re going to modify those systems to maintain egress, or plan an ILSM on how staff, patients, and visitors move around the space in the short-term.
Tyler: Issuing ILSM documentation is a function of the hospital, but its successful creation relies on a team approach. Hagerman’s knowledge of maintaining compliance provides additional value to the client, from our early involvement in upfront planning to assisting with plans that help the safety officers implement training.
What resources or information should healthcare organizations look to or have at the ready to prepare them for their construction projects?
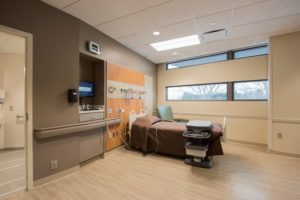
Ben: If possible, hospitals should engage third-party consultants to complete life safety reviews prior to Joint Commission reviews. Renovating a hospital to meet Joint Commission standards is not always easy. During a renovation, you will likely run into unforeseen conditions that need corrections, but with renovations it’s also important to inspect during the construction process to minimize issues when it is completed. Whether it is an added outlet or additional cable run as contractors get back into the ceilings, it’s important to monitor that work to make sure they are not creating issues with the later installations.
Tyler: Clients should have current life safety and as-built plans available to review during any renovation work. It’s important to always understand when rated walls are affected, and it’s critical to have updated MEP drawings when planning for shutdowns.
What trends or new developments are available to owners and/or design and construction teams to help foster safety of users during a renovation or expansion?
Ben: The use of manufactured ICRA panels—like EDGE Guard or similar systems—are becoming more popular than built-in-place drywall systems. Hospitals often require drywall partitions to be finished and painted, which creates additional dust and issues for patients in critical areas. Modular systems are installed in less time, require no finishes, and can be easily cleaned. While the manufactured ICRA panels may not have the sound-absorbing properties of a drywall system, in areas that are highly sensitive to noise, like neonatal intensive care units, we can add sound-deadening walls on the construction side of the barrier. This leaves potential dust and drywall in our controlled, negative air environment.
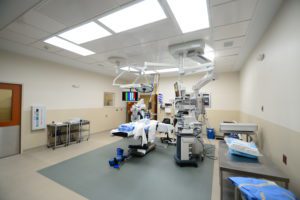
Tyler: Remote pressure monitoring technology allows project members to view and confirm pressure relationships are correct by simply picking up a phone or opening a laptop. These systems also keep clear records of pressure relationships throughout a project for easy-to-access documentation.
Jay: Tools such as HEPA vacuums help clean workers prior to leaving the construction area, and new tools can reduce noise and vibration when working around high-risk areas.
What are some insightful approaches you’ve seen hospitals or healthcare organizations take as it relates to keeping their caregivers, patients and visitors informed during a construction project?
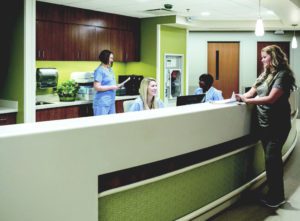
Tyler: From the front desk to the nurses, all staff affected by significant projects or outages should be involved during the planning stages. This brings ownership of the plan to all involved and results in better implementation. Communication needs to go beyond an email and should include follow-up with department managers to make sure staff are aware and up-to-date.
Ben: If developing the plan is step one, communicating it with hospital staff is step two. The more aware they are of construction plans, the better. Staff members appreciate the information, and effective communication benefits both the schedule and the budget. On my projects, we have weekly owner/architect/contractor meetings for planning future utility shutdowns, egress impacts, or departmental impacts that may require relocating staff and patients. These plans are issued to the rest of the hospital staff through emails, letters, and on-site signage. Even with that level of communication and discussing these items months prior to starting, there can still be challenges. Hospital staff members have important responsibilities and may not be comfortable with construction terminology. To assist with this, superintendents and on-site crews need to become familiar with hospital staff and should check in with them often to communicate our progress and see if they have any concerns.
Is there anything else hospitals should be aware of prior to embarking on a facility renovation project?
Jay: Hospitals should be aware of the dangers of Legionella—a bacteria that can cause a serious type of pneumonia—and ways to mitigate it. Legionella can grow in environments where water sits for a long period of time, such as when plumbing is shut off for a construction project. When released into the air, it poses a danger to people with weakened immune systems and can cause a serious type of pneumonia. By collaborating with the hospital and partnering with a water management company, Hagerman can add value to the process of creating a water management plan that considers those risks and how to address them. For 24/7 facilities, effective planning, communication, and training has to be in place for every shift. When thinking about how people will move through the facility, it’s also important to remember that not everyone will be walking—some will be in hospital beds and wheelchairs. In addition, the phasing plan should address how materials will enter and exit the building.
While there are certainly complexities to renovating and expanding healthcare facilities, the positive outcomes of an improved patient, family, and staff environment make it all worthwhile. If you’d like to engage an experienced contractor in your upcoming healthcare facility project, please contact us today.